Waterjet cutting for steel & aluminium - PREMIUM WATERCUT
You are looking for a waterjet cutting service? ABRAMS Industries® offers you exactly this service.
We have specialised on Premium waterjet cutting for steel & aluminium.
We not only offer our own PREMIUM-Metals but also apart from our product portfolio other steel and aluminium grades, dimensions and specifications too. As well you are able to send us your steel and aluminium plates and use us as a subcontractor.
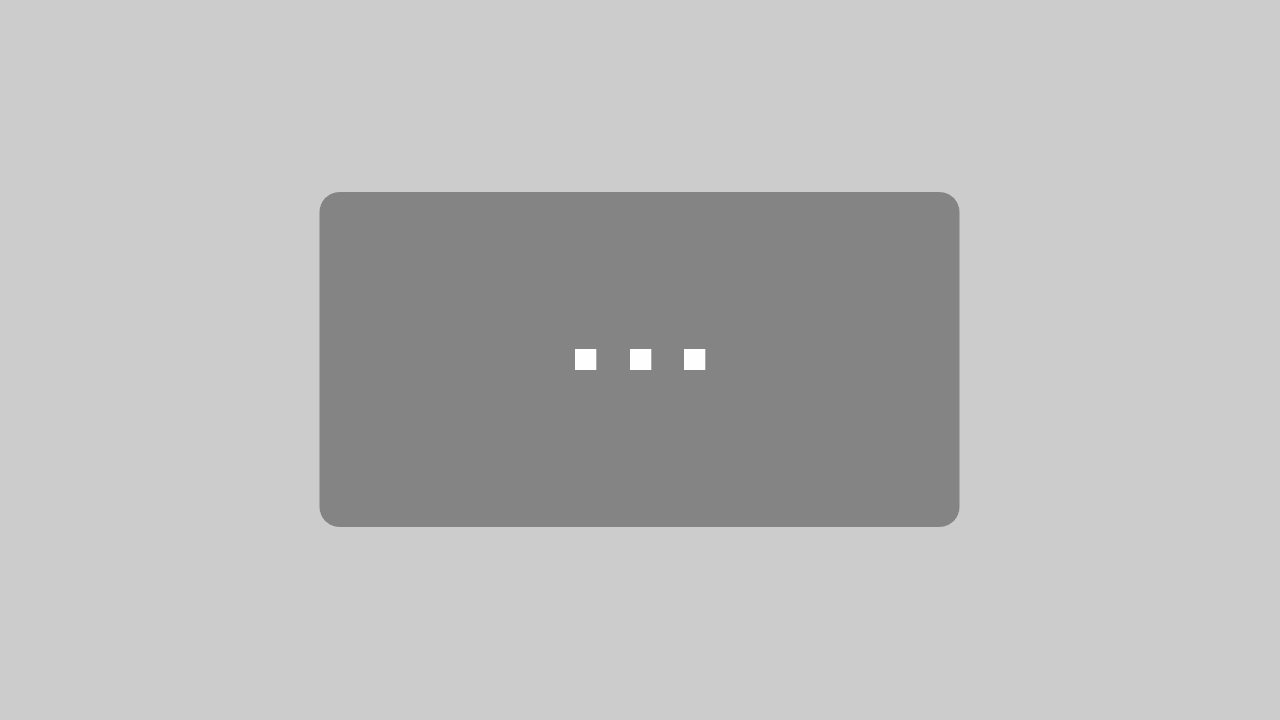
By loading the video, you agree to YouTube's privacy policy.
Learn more
What thickness are steel and aluminium allowed to have?
Below you will find the applicable maximum dimensions and tolerances:
Maximum thickness:
• Steel up to 100 mm
• Aluminium up to 200 mm
Formates:
• Precision Steel
• Sheet and plate material
• Round material (round blanks, rings and many more)
• According to drawings Prototype or small series production
Tolerances steel & aluminium:
• +/- 0,1 mm possible (depending on material thickness)
• Also with cutting compensation on request
Additional services:
• Preparation of measuring protocols
• Labelling with needle embosser
• Trowalising (vibratory grinding / deburring)
The maximum thickness when waterjet cutting depends on the material and the cutting quality needed. With ABRAMS Industries® we can effectively cut steel up to a thickness of 100 mm and for aluminium up to 200 mm.
We are happy to cut tool steel, structural steel, stainless steel, high-speed steel (HSS), case-hardening steel, tempered steel, nitrided steel, hardened steel and aluminium for you.
For specific requirements, it is worth seeking individual advice. Discover the numerous possibilities for your project!
Advantages of waterjet cutting
Waterjet cutting offers numerous technical and environmental advantages making it a prevered choice for industries and manufacturing.
- Precision: cutting quality - less post processing required
- Cutting edge quality: clean and smooth cutting edges
- Cold processing: No heat zones and hardening (surface layer)
- Material optimisation: low waste
- No material impact
- No material stress
- No structural change or material deformation
- Versatile: almost all materials
- Environmentally friendly: less waste - no harmful chemicals or gases
To summarise, water cutting is an exceptionally flexible and precise technology that is suitable for a wide range of applications and materials, while being environmentally friendly and resource-saving.
What is waterjet cutting?
Waterjet cutting is a precise technique for cutting various materials without affecting them thermally. The material is cut using a high-pressure water jet and an abrasive. Thanks to the abrasive, the water jet can also cut harder materials such as metal or hardened steel.
This prevents material changes such as warping or thermal damage, which can occur with other cutting processes such as laser cutting or plasma cutting.
Premium waterjet cutting with 2D cutting head technology
ABRAMS Industries® offers 2D cutting head technology with angle compensation for optimum adjustment of the cutting bevel.
As the cutting speed increases, the water jet has a stronger trailing effect when cutting the material and runs at an angle downwards (angular error). This results in unclean corners, cutting bevels, rough surfaces and rounded corners and holes.
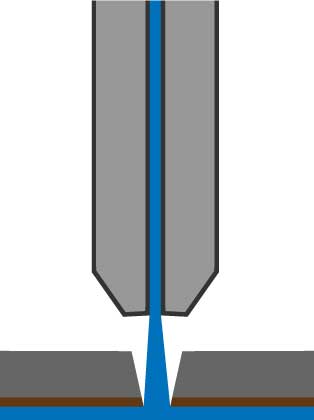
The two main processes for waterjet cutting
There are two main types of waterjet cutting:
Pure waterjet cutting
Pure waterjet cutting involves only water without an abrasive being pressed through a very small nozzle under extremely high pressure. This can result in a pressure of up to 6.000 bar or more. This cutting process is used for softer materials such as paper, rubber, some plastics or textiles.
Abrasive waterjet cutting
When waterjet cutting with abrasives, an abrasive (cutting agent), such as garnet sand, is added to the water. This addition enables the waterjet to cut even high-strength, thick, demanding and tensile strong materials such as steel or aluminium.
Quality levels for waterjet cutting - Q1 to Q5
The Quality Levels - Q1 to Q5
The quality of the individual cut when waterjet cutting can vary depending on the application and is categorised into different quality levels.
At ABRAMS Industries® we usually offer a Q3 cut quality, the so-called production or standard cut. Of course, all quality levels from Q1 – Q5 are also possible on request.
These five levels define the precision and surface quality of the cut. The higher the quality level, the lower the surface roughness and therefore the finer the surface finish. Each quality level has specific characteristics.
Therefore, the choice of quality level depends on the specific requirements of the project, including the desired precision, material type and cost efficiency.
Quality level - Q1
separating cut / rough cut
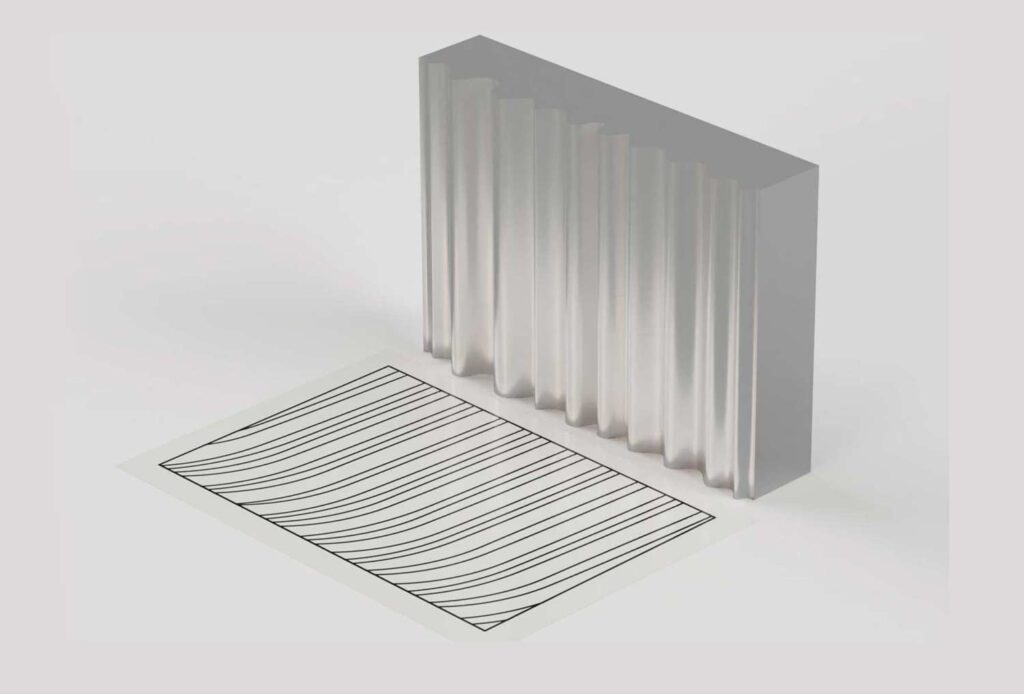
Application:
Q1 is suitable for fast and rough cuts where the cutting quality is of secondary importance.
Characteristics:
Higher cutting speed, but rougher surface and greater tolerances. Ideal for preliminary cuts or when subsequent machining is required.
Quality 1 = separating cut
Quality grade - Q2
Coarse cut
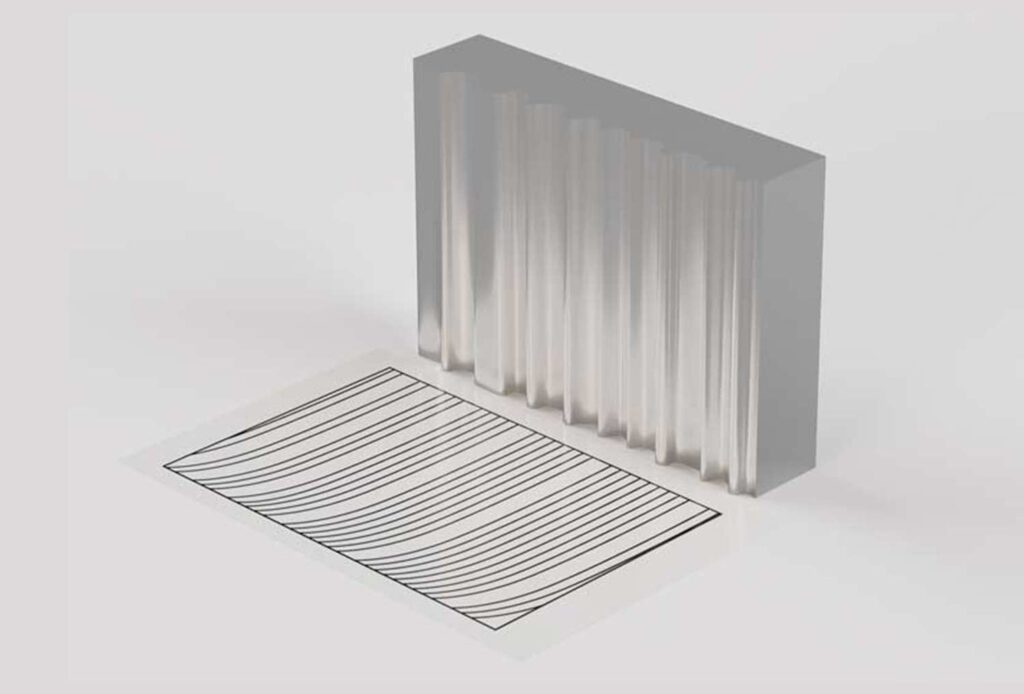
Application:
Q2 is suitable for general applications where an appropriate cutting quality is required.
Characteristics:
Medium cutting speed with better surface quality and accuracy than Q1, but still visible streaks.
Quality 2 = Coarse cut
Quality level - Q3
standard cut / production cut
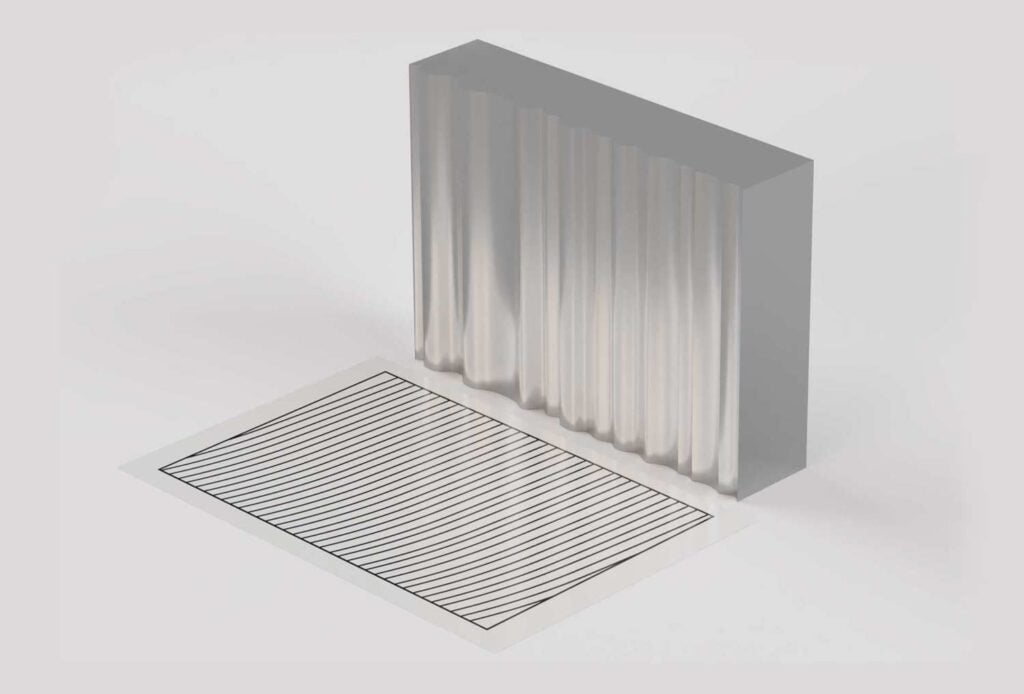
Application:
Q3 is ideal for applications that require high precision and a good surface finish.
Characteristics:
Reduced cutting speed for improved precision and surface finish. Reduced striations and tight tolerances thanks to increased accuracy.
Quality 3 = standard cut
Quality level - Q4
Quality cut
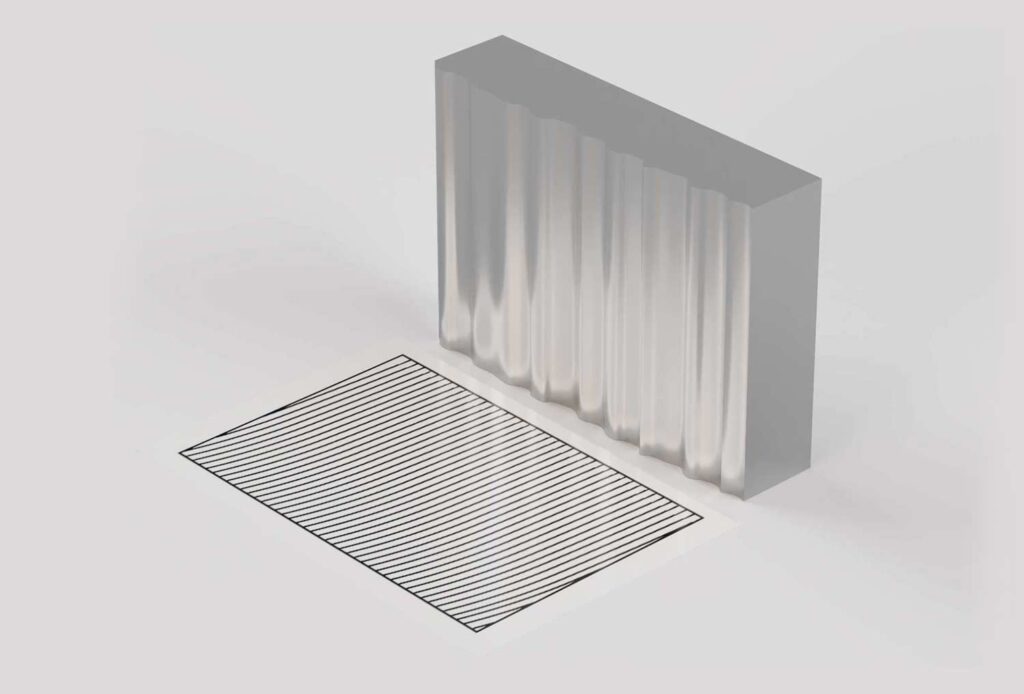
Application:
Q4 is ideal for high-precision applications where a very good surface finish is required.
Characteristics:
Slower cutting speed, which enables excellent surface quality and very tight tolerances. Minimal chipping.
Quality 4 = quality cut
Quality level - Q5
Best cut / precision cut
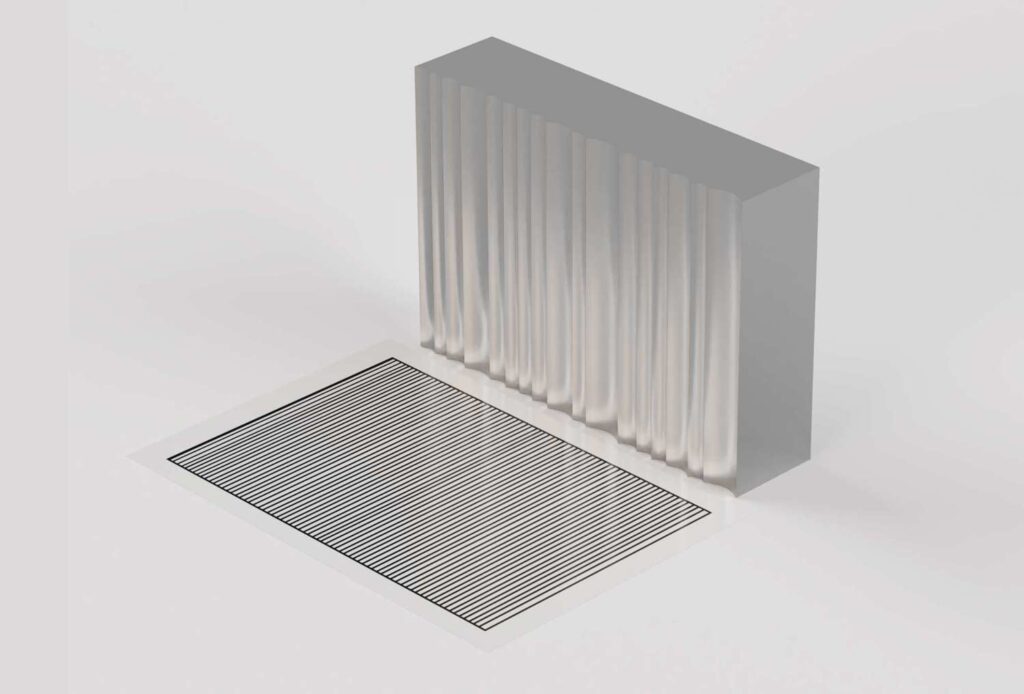
Application:
Q5 is ideal for applications that require the highest precision and surface quality.
Characteristics:
Very slow cutting speed, resulting in an excellent surface finish with virtually no streaks. Suitable for the finest contours and most complex shapes.
Quality 5 = Best cut
FAQ - Questions about waterjet cutting
How does CNC waterjet cutting actually work?
CNC waterjet cutting uses a high-pressure jet of water to cut materials precisely. The water jet is channelled through a narrow nozzle and often mixed with abrasives such as garnet sand. This greatly increases the cutting ability of the water jet.
This technology makes it possible to produce complex moulds from a variety of materials without thermal stress and high precision. Waterjet cutting is ideal for projects where accuracy and material integrity are paramount.
Discover the precision of waterjet cutting for your next project with ABRAMS Industries®!
What does waterjet cutting cost?
The cost of waterjet cutting varies depending on material thickness, complexity of the cut and material type. It offers a cost-effective alternative for high-precision cuts without material distortion. Get a personalised quote straight away and experience the cost-effectiveness of waterjet cutting!
The price of watercutting depends on the following factors:
• Cost of the base metal
• Procurement costs, where applicable
• Material thickness
• Cut quality (Q1 to Q5)
• Length and number of contour cuts
Which materials can be cut by waterjet cutting?
Waterjet cutting can be used to process almost all materials such as metals, plastics, glass, ceramics, stone and much more. This versatility makes it a favoured method for industries that need to precisely cut different and even hard materials. Perfect for customised solutions in design and manufacturing.
Expand your production possibilities with waterjet cutting and take your production to the next level!
Which file format is required for waterjet cutting?
Vector graphics in formats such as DXF, DWG or SVG are primarily used for waterjet cutting. These formats enable precise cuts and complex design realisations. Waterjet cutting therefore impresses with particularly short programming and set-up times. The following files are suitable for data transfer:
• PDF
• DXF
• STEP
• DWG
• EPS
• BMP
• (further formats on request)
To achieve optimum results, make sure that your files are in one of these formats. If you have any questions, please contact us or get started now!
Is a weld seam preparation possible with a waterjet cutting system?
Waterjet cutting systems can be used effectively for weld seam preparation by cutting precise edges and profiles required for an optimal welded joint. The prerequisite is that the machine is equipped with a 3D cutting head.
This technology reduces post-processing time and improves the quality of the weld seams. Use waterjet cutting for seamless integration into your production processes!
Waterjet cutting vs. plasma cutting and flame cutting
Compared to plasma cutting and oxy-fuel flame cutting, waterjet cutting offers better cutting quality and minimises post-processing.
Waterjet cutting avoids thermal stress and enables more precise cuts. It therefore enables better contour accuracy and no discolouration occurs on the cut edges. In addition, waterjet cutting processes a wider range of materials and works with almost any material.
ABRAMS® PREMIUM WATERCUT – An upgrade for your production line!
Laser cutting vs. water jet cutting
In contrast to laser cutting, waterjet cutting can be used universally and is suitable for a wider range of products. Unlike laser cutting, waterjet cutting does not cause thermal damage. It is ideal for applications where precision and material integrity are crucial.
It also allows thicker materials to be cut, meaning that sheets can be cut in packs, which is not possible with a laser. This makes waterjet cutting an economical cold cutting process for companies.
Despite its many advantages, waterjet cutting also has some disadvantages.
• Usually slower cutting speeds
• Water disposal due to high environmental requirements
• Noise development
To summarise, waterjet cutting is an excellent alternative to laser cutting, as laser cutting is limited to just a few metals. It is particularly suitable for thick materials such as steel and aluminium, as the thicker the material, the more economical waterjet cutting becomes.
Combine precision with flexibility and protect the material – waterjet cutting!
How accurate is waterjet cutting?
Waterjet cutting achieves accuracies in the range of ±0,1 mm, depending on the system, the settings and the selected quality level. The cut surface of the metal is slightly rough to smooth and precise, with minimal burr formation. Perfect for high-quality end products.
Strive for perfection – with waterjet cutting!
Can customer requirements be taken into account for waterjet cutting?
Waterjet cutting is extremely adaptable, meaning that specific customer requirements and complex designs can be realised. Individualised material processing is of course possible, which makes the ABRAMS® PREMIUM WATERCUT service a flexible solution for customized projects.
Design the project according to your ideas with waterjet cutting!